Einer der Herstellungsprozesse bei der Betonsteinproduktion, der noch immer nicht automatisiert ist, ist die Qualitätskontrolle der Produkte.
Eine Möglichkeit zur Automatisierung dieses Produktionsbereichs besteht in der automatischen Erkennung von Defekten und Erfassung von Daten. Dies geschieht durch intelligente Geräte auf Basis maschinellen Sehens.
Vorteile der Automatisierung und des Einsatzes von Bildverarbeitungssystemen bei der Betonsteinproduktion
Der Einsatz von Bildverarbeitungssystemen ermöglicht:
- Daten aus allen wichtigen Produktionsbereichen automatisch erfassen, d. h. der gesamte Produktionsprozess kann digitalisiert und alle Daten analysiert werden. Basierend auf den über einen langen Zeitraum gesammelten Daten ist es möglich, die problematischsten Chargen in Bezug auf Defekte und Höhenabweichungen zu identifizieren. Wenn eine bestimmte Form mehr Defekte aufweist, muss sie wahrscheinlich bereits repariert oder ersetzt werden;
- den Prozess der Materialabrechnung und -abschreibung basierend auf dem tatsächlichen Produkt- und Materialfluss vereinfachen;
- die durchschnittliche Höhe von Produkten nach Produkttyp automatisch verfolgen und an der Reduzierung der Gesamthöhe arbeiten, um die Materialkosten zu senken. Dies sind ziemlich erhebliche Kosteneinsparungen. Wenn Sie beispielsweise 60 mm große Produkte mit einer durchschnittlichen Höhe von sogar 59 mm statt 61 mm formen, sind dies 3 % des gesamten Materialvolumens.
- die Ergebnisse der Arbeit der Bediener sehen und rechtzeitig zusätzliche Schulungen durchführen;
- das Arbeitstempo analysieren, Ausfallzeiten identifizieren und deren Ursachen beseitigen und so die Gesamtproduktivität steigern.
Darüber hinaus können durch die Echtzeitüberwachung aller Erzeugnisse die Produktionskosten erheblich gesenkt werden und der Anteil fehlerhafter Produkte verringert werden.
Technologien wie maschinelles Sehen und künstliche Intelligenz helfen bei der Steuerung der Produktion. Aber meist nur auf der trockenen Seite. Sehen Sie, wie es umgesetzt wird:
Inspektion auf der Trockenseite des Förderers
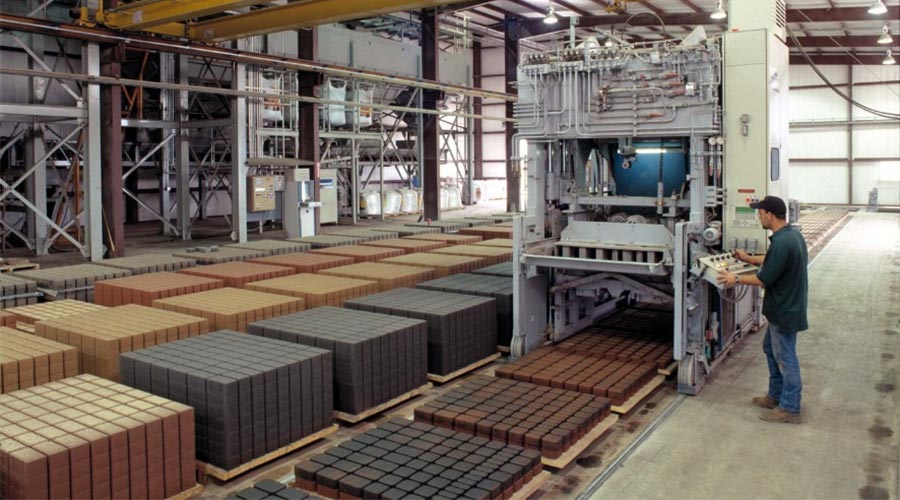
Kontrolle auf der Trockenseite des Förderers zur Reduzierung von Mängelansprüchen
Ein intelligentes System protokolliert, welche Fliesen der Kommissionierer von der Palette genommen hat und stellt sicher, dass alle defekten Steine ersetzt werden und keiner davon zum Kunden gelangt.
Wenn wir die Anzahl aller entfernten Steine kennen, können wir das Volumen der Betonmischungsverluste für jede Charge separat automatisch berechnen.
Wenn wir nur die Trockenseite der Produkte kontrollieren, kennen wir die Gründe für fehlerhafte Produkte und Verluste nicht und können die Häufigkeit der Fehler nicht analysieren. Deshalb ist die wichtigste Aufgabe die Inspektion der Nassseite des Förderbands.
Inspektion auf der Nassseite des Förderers
Auf der Nassseite das Bildverarbeitungssystem
- jede Fliese auf einer Palette in Echtzeit mit einer Genauigkeit von 1 mm messen;
- Defekte in der Oberfläche der Fliese, wie etwa Risse, Absplitterungen, Schalen, erkennen;
- Kontrollieren Sie die Konformität der Farbe der Partei.
Der Bediener der Betonformmaschine kann diese Informationen nutzen, um Probleme mit Formprodukten schnell zu erkennen und Maßnahmen zu ergreifen, um die Herstellung fehlerhafter Produkte zu verhindern.
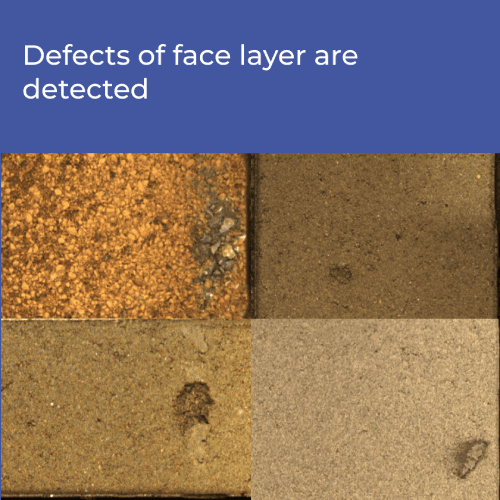
Von QuatroPBC erfasste Defekte auf der Oberseite einer Fliese
und erfüllt zwei wichtige Funktionen:
- Sammeln von Daten zum Herstellungsprozess;
- Verhindern der Herstellung fehlerhafter Produkte und Reduzieren direkter Verluste.

Bericht von der QuatroPBC-Schnittstelle
Eine der Funktionen eines Qualitätskontrollsystems QuatroPBC ist die Sammlung von Daten zur weiteren Analyse:
- Produktidentifikation - Erkennung von Form und Farbe. Diese Informationen sind für die korrekte Chargenbildung der Produkte erforderlich;
- Pflege eines Fotoarchivs aller produzierten Paletten. Eine sehr nützliche Funktion, um zu verstehen, was uns nach einer Nachtschicht oder nach einem Wochenende beim Rollout erwartet.
- Aufzeichnung der Produktionszeit jeder Palette auf die Sekunde genau – zur Verfolgung von Mikroausfällen der Ausrüstung.
Sämtliche Palettenfotos und Messergebnisse werden in einem Produktionsbericht nach Charge, Produkteigenschaft, Bediener oder Schicht zusammengefasst.
Im Archiv sind von jeder Palette großformatige Bilder gespeichert, so dass jederzeit ersichtlich ist, wer genau was früher geformt hat und welche Probleme dabei auftraten.
Auf die Schnittstelle kann nicht nur der Bediener, sondern auch alle für die Produktion verantwortlichen Mitarbeiter zugreifen. Sie können in Echtzeit sehen, was genau gerade oder zu jedem anderen Zeitpunkt an der Linie passiert.
Technologie der Qualitätskontrolle von QuatroPBC
Die Palette bewegt sich auf dem Förderband unter dem intelligenten Gerät hindurch. Die empfangenen Daten werden in Echtzeit analysiert und an den Bediener übermittelt.
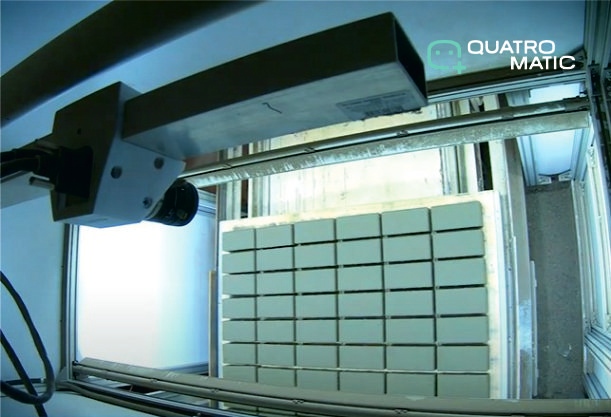
So funktioniert QuatroPBC
Und erst danach werden die folgenden Aufgaben korrekt ausgeführt: Nach der Festigkeitszunahme werden die Produkte auf die Trockenseite ausgerollt, und dort ist es mit Hilfe der in der Palette installierten RFID-Tags möglich, jede Palette zu identifizieren und festzustellen, welche Abweichungen auf der Nassseite festgestellt wurden.
Bei Bildverarbeitungssystemen in der Produktion geht es nicht nur darum, hier und jetzt Defekte zu erkennen, sondern vielmehr darum, große Datenmengen zu sammeln, deren Analyse die Produktionseffizienz in unseren schwierigen Zeiten deutlich steigern kann.
Haben Sie Fragen zu QuatroPBC? Stellen Sie Ihre Frage im untenstehenden Formular!